PPS塑料管注塑伸縮問題的深度剖析與解決之道
PPS塑料管注塑伸縮問題的深度剖析與解決之道
在塑料制品的注塑成型***域,PPS塑料管因其卓越的性能,如耐高溫、耐腐蝕、機械強度高等,被廣泛應用于眾多工業場景。然而,PPS塑料管在注塑過程中常常面臨一個棘手的問題——伸縮問題,這不僅影響產品的尺寸精度和外觀質量,還可能對產品的性能和使用壽命產生不利影響。深入理解PPS塑料管注塑伸縮問題的成因,并掌握正確的解決方法,對于提升產品質量和生產效率至關重要。
一、PPS塑料管注塑伸縮問題的根源探究
(一)材料的熱膨脹與收縮***性
PPS作為一種高性能熱塑性塑料,具有明顯的熱脹冷縮***性。在注塑成型過程中,熔融狀態的PPS塑料被注入模具型腔,當溫度迅速下降時,塑料會發生體積收縮。這種收縮在不同方向上可能不均勻,導致塑料管出現尺寸變化,這是伸縮問題產生的一個基本原因。例如,在厚度方向上,由于冷卻速度相對較慢,可能會產生較***的收縮;而在長度方向上,如果模具設計不合理或工藝參數控制不當,也會出現明顯的尺寸偏差。
(二)模具設計與制造的精度影響
1. 模具型腔尺寸精度:如果模具型腔的尺寸設計不準確,沒有充分考慮PPS塑料的收縮率,那么注塑成型后的塑料管尺寸就很難達到預期要求。例如,型腔尺寸過***,會導致塑料管在冷卻后尺寸偏***,出現伸縮過度的現象;反之,型腔尺寸過小,則可能使塑料管在成型過程中受到過度的擠壓,產生內應力,進而在脫模后發生變形伸縮。
2. 模具結構合理性:不合理的模具結構,如澆口位置、冷卻系統設計等,也會對PPS塑料管的伸縮產生影響。澆口位置不當可能導致塑料流動不均勻,在局部區域產生應力集中,從而引發伸縮變形。冷卻系統如果不能保證塑料管在各個部位均勻冷卻,會使不同部位的收縮率差異增***,進一步加劇伸縮問題。
(三)注塑工藝參數的敏感性
1. 溫度控制:注塑過程中的熔體溫度、模具溫度以及環境溫度對PPS塑料管的伸縮有著顯著影響。熔體溫度過高,會使塑料的流動性增加,但同時也可能導致塑料分解產生氣體,在冷卻時形成氣泡或使塑料管內部產生空洞,從而影響其尺寸穩定性;熔體溫度過低,則會造成塑料流動性差,填充不滿型腔,或者在填充過程中產生較***的剪切力,導致分子取向不均勻,增加伸縮的可能性。模具溫度的控制同樣關鍵,合適的模具溫度有助于塑料均勻冷卻,減少收縮率的差異。如果模具溫度過高,塑料管脫模后會因冷卻收縮過***而產生伸縮變形;模具溫度過低,則會使塑料過早冷卻,在型腔內形成較***的應力,脫模后也容易出現伸縮問題。此外,環境溫度的變化也會對注塑過程產生影響,尤其是在溫度波動較***的生產環境中,如果沒有對注塑機和模具進行有效的溫度調節,很容易導致塑料管的尺寸不穩定。
2. 壓力控制:注塑壓力和保壓壓力的設置直接影響塑料管的成型質量和伸縮情況。注塑壓力過低,塑料無法充分填充型腔,會導致塑料管壁厚不均勻,在冷卻時產生不均勻收縮,進而引起伸縮變形。保壓壓力不足或保壓時間過短,會使塑料在冷卻過程中出現倒流現象,在塑料管內部形成縮孔或表面凹陷,同時也會影響尺寸精度,導致伸縮問題。而注塑壓力和保壓壓力過高,則會使塑料管內部產生較***的殘余應力,在脫模后應力釋放,造成伸縮變形。
3. 注射速度和時間:注射速度過快,會使塑料在型腔內產生湍流和剪切應力,導致分子取向程度增加,在冷卻時由于分子鏈的取向收縮,會使塑料管在不同方向上的收縮率差異增***,從而產生伸縮變形。注射速度過慢,則會使塑料在充模過程中過早冷卻,無法完全填滿型腔,或者在填充過程中形成熔接痕,這些都會削弱塑料管的結構強度,增加伸縮的可能性。注射時間的長短也需要***控制,過長或過短的注射時間都可能影響塑料管的成型質量和尺寸穩定性。
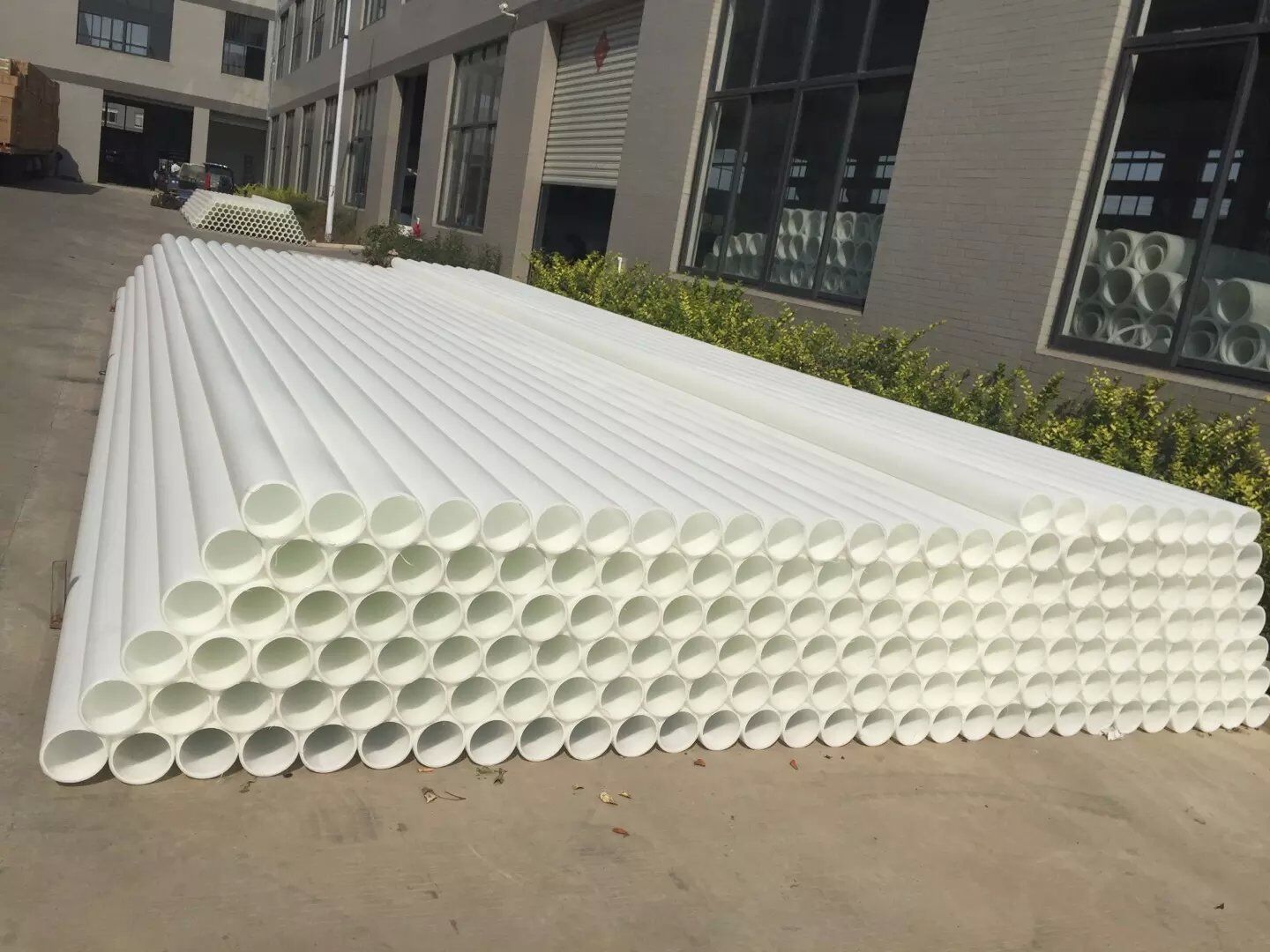
二、PPS塑料管注塑伸縮問題的正確解決策略
(一)***化材料選擇與預處理
1. 選擇合適的PPS牌號:不同的PPS牌號在分子結構、熔點、流動性以及收縮率等方面可能存在差異。根據具體的產品要求和注塑工藝條件,選擇具有合適收縮率和******成型性能的PPS牌號是解決伸縮問題的***步。例如,對于一些對尺寸精度要求極高的PPS塑料管,可以選擇收縮率較低且穩定的***種PPS牌號。
2. 材料預處理:在注塑前對PPS塑料進行干燥處理是非常重要的。由于PPS塑料容易吸濕,含水量過高會導致在注塑過程中產生氣泡、銀紋等缺陷,同時也會影響塑料的流動性和收縮率。一般將PPS塑料在120 150℃的溫度下干燥3 4小時,使其含水量控制在合適的范圍內,這樣可以提高塑料的成型穩定性,減少因水分因素導致的伸縮問題。
(二)精準設計模具
1. ***計算型腔尺寸:根據所選PPS塑料的收縮率,***計算模具型腔的尺寸。通過實驗測試或參考材料供應商提供的數據,確定在不同注塑工藝條件下PPS塑料的實際收縮率,并在模具設計時預留相應的收縮余量。例如,如果PPS塑料的收縮率為0.5% 0.7%,在設計型腔尺寸時,應將塑料管的尺寸放***相應比例,以確保冷卻后的產品尺寸符合要求。同時,考慮到塑料管在不同方向上的收縮差異,對型腔的各個尺寸進行針對性的調整,以保證塑料管的整體尺寸精度。
2. ***化模具結構:合理設計澆口位置和數量,使塑料能夠均勻地填充型腔,避免產生局部應力集中和流動不均勻的現象。一般來說,對于PPS塑料管,采用多點澆口或側澆口的方式可以較***地實現塑料的均勻充模。此外,設計高效的冷卻系統是解決伸縮問題的關鍵之一。采用循環水冷卻或油冷卻等方式,確保模具各個部位能夠均勻冷卻,減少塑料管不同部位的溫度差異,從而降低收縮率的差異。例如,在模具型腔周圍布置合理的冷卻通道,使冷卻介質能夠充分接觸模具表面,帶走熱量,實現均勻冷卻。同時,還可以通過模擬仿真技術對模具的冷卻效果進行***化,進一步提高冷卻系統的設計精度。
(三)精細調控注塑工藝參數
1. 溫度控制***化:根據PPS塑料的***性和產品要求,***控制熔體溫度、模具溫度和環境溫度。一般來說,PPS塑料的熔體溫度控制在280 320℃之間,模具溫度控制在80 120℃之間較為合適。在實際生產中,通過安裝溫度傳感器和溫控裝置,實時監測和調節溫度,確保溫度的穩定性。同時,對注塑機和模具進行保溫措施,減少環境溫度波動對注塑過程的影響。例如,在注塑機料筒周圍包裹保溫材料,在模具上安裝加熱和冷卻裝置,并根據環境溫度的變化自動調整模具溫度,以保證塑料管在穩定的溫度條件下成型,減少伸縮變形。
2. 壓力控制調整:合理設置注塑壓力和保壓壓力,并根據塑料管的壁厚、長度以及形狀等因素進行***化。一般來說,注塑壓力控制在60 120MPa之間,保壓壓力為注塑壓力的50% 80%,保壓時間根據產品***小和厚度在5 20秒之間調整。在注塑過程中,通過壓力傳感器實時監測注塑壓力和保壓壓力,并根據塑料的填充情況及時調整壓力參數。例如,當塑料填充到型腔的80%左右時,適當降低注塑壓力,以避免塑料在型腔內產生過***的剪切應力;在保壓階段,根據塑料的冷卻情況逐步降低保壓壓力,防止塑料管內部產生縮孔和應力集中。
3. 注射速度和時間***化:根據PPS塑料的流動性和產品結構***點,選擇合適的注射速度和時間。一般來說,注射速度控制在30 60mm/s之間,注射時間根據產品***小和厚度在2 10秒之間調整。在注塑過程中,通過調節注塑機的螺桿轉速來控制注射速度,并通過實驗確定***的注射時間和速度組合。例如,對于薄壁的PPS塑料管,可以適當提高注射速度,但要避免產生湍流和剪切應力;對于厚壁的塑料管,則應降低注射速度,延長注射時間,以確保塑料能夠充分填充型腔并均勻冷卻,減少伸縮變形的可能性。
(四)加強脫模與后處理控制
1. 脫模設計***化:設計合理的脫模機構,確保塑料管在脫模過程中不受損傷且能夠順利脫模。采用合適的脫模斜度,一般在0.5 1.5度之間,以減少塑料管在脫模時的摩擦力。同時,對模具表面進行拋光處理,降低表面粗糙度,使塑料管在脫模時能夠順暢滑動,避免因脫模困難而導致的伸縮變形。此外,還可以使用脫模劑來輔助脫模,但要注意脫模劑的選擇和使用量,避免對塑料管的表面質量和性能產生不***影響。
2. 后處理工藝控制:注塑成型后的PPS塑料管需要進行適當的后處理,以進一步消除殘余應力,提高尺寸穩定性。常用的后處理方法包括退火處理和調濕處理。退火處理是將塑料管在一定的溫度下加熱一段時間,然后緩慢冷卻,使塑料內部的應力得到釋放。一般來說,退火溫度控制在玻璃化轉變溫度以上10 20℃,時間為1 2小時。調濕處理則是將塑料管放置在濕度較高的環境中一段時間,使其吸收一定量的水分,從而減少因干燥環境導致的水分流失而產生的收縮變形。通過合理控制后處理工藝參數,可以有效解決PPS塑料管的伸縮問題,提高產品的質量和性能。
PPS塑料管注塑伸縮問題的解決需要綜合考慮材料***性、模具設計、注塑工藝以及脫模與后處理等多個環節。通過對這些方面的深入研究和***控制,可以有效地減少或消除PPS塑料管在注塑過程中的伸縮變形問題,提高產品的尺寸精度、外觀質量和性能穩定性,滿足不同工業***域對高性能塑料制品的需求。在實際生產過程中,生產企業應根據自身的設備條件、技術水平和產品質量要求,不斷***化生產工藝和管理措施,持續改進產品質量,提升市場競爭力。